Light... let's always support, love, and care for one another, and always make light.
{The news this morning is sickening, yet again, and so I push myself to look beyond the grief, sadness, frustration, anger and darkness, to seek light, celebrate the strength of constructive, kind, inspiring, creative, beneficial activities. And from a post my friend, Carol, shared, this
Billy Crystal quote, resonates even more... "Build bridges between people, not walls."}
We are preparing for the North County Mini Maker Faire... and it's like a beautiful, and wild mania around BOoM Town! We want to bring our best to share with the Faire, to inspire, to enjoy. We have almost as many works in progress, as old favorites. And we have many,
many old favorites that need tune-ups, repairs, and updates, too. Honestly, it's probably more than we can complete, but we are trying, and we like to savor and celebrate the process, the journey, as much at the destination. Yesterday we were fully engaged with old, and new making, and loving it...

We collect and gather supplies from thrift shops, from curbs and dumpsters, from our awesome cousins' market! Recently, my uncle lent me his truck so Alex and I could haul home all the wood pallets my cousins shared with us. Now we have great wood to salvage for sculpting, and constructing. This day, the wood is being disassembled, cut, planed, sanded and stained to make a box.
What's the box for? The box is for an interactive
Makey Makey garden!
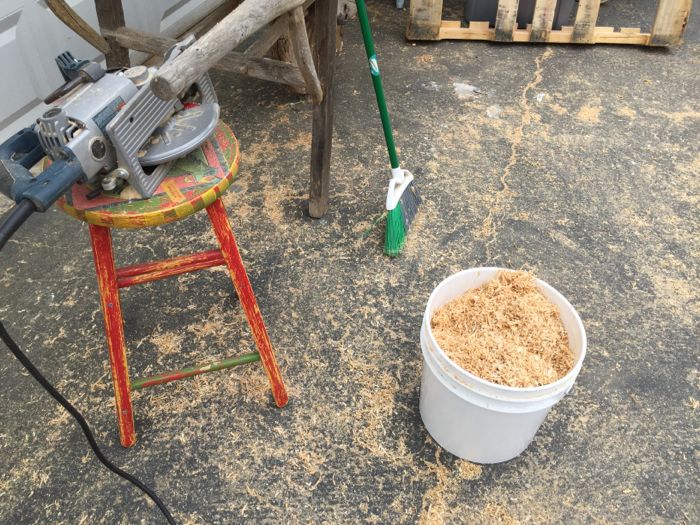
The making Alex and James were doing, was inspiration for the making Maria and jumped into! All of this sawdust sent me into the house to look for wax. We discovered some really clever and effective fire starters back in the day, when we were camping at El Capitan State Beach, and so Maria and I decided to start our own cottage industry.
Fire Starters...
Supplies...
A double boiler
Tiny paper cups
Wax
Wood shavings
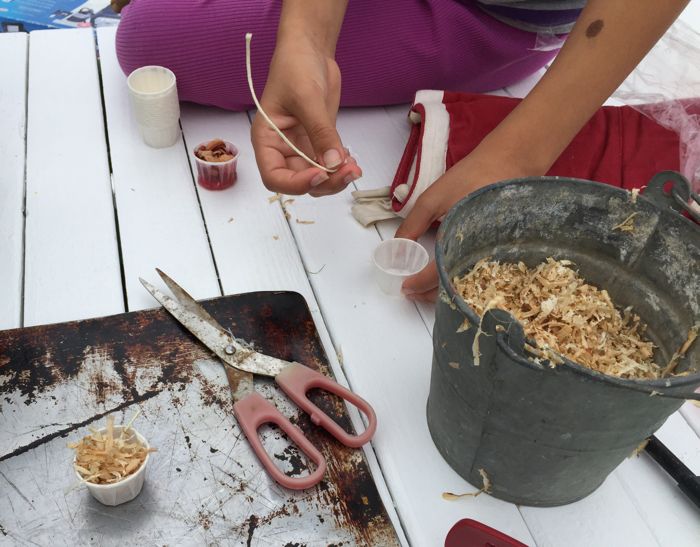
Our wax is from beeswax sheets we crafted with years ago. I raided our candle drawer and decided it was time to repurpose some of these old beauties. We pulled out the wicks, which we decided to cut up and use with the fire starters. (They don't need wicks, but we like the idea of not wasting them, and maybe they will prove to be an improvement.) Tiny paper cups are from a restaurant supply store, and can
be fun and useful for a little baking, too.
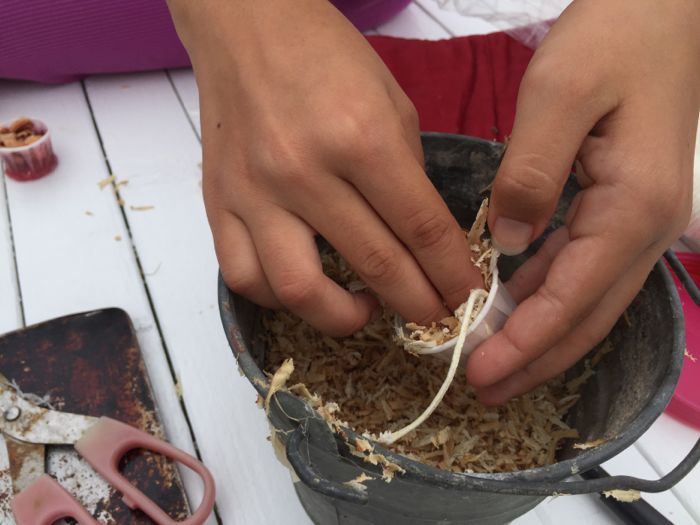
The wicks go into the cups, along with wood shavings, or fine wood chips. Then we pour the melted wax into each cup, sealing the wood shavings, leaving the wick end exposed.
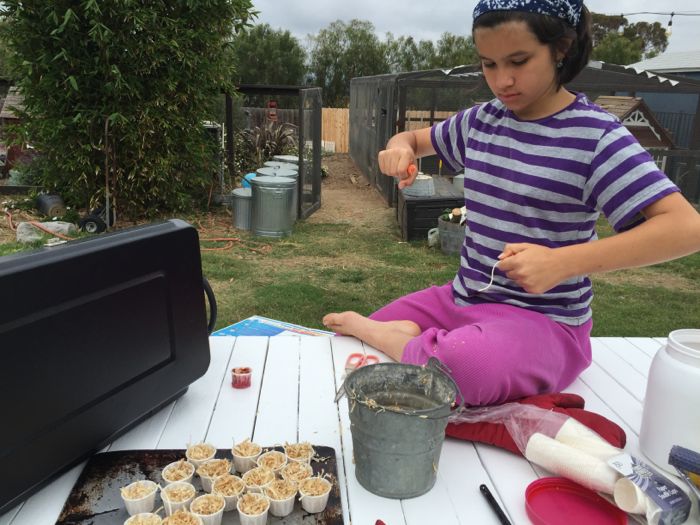
Our first batch of wax was all colors and looked like weak coffee. Then Maria decided to separate the colors, so we made yellow, blue, and orange fire starters.
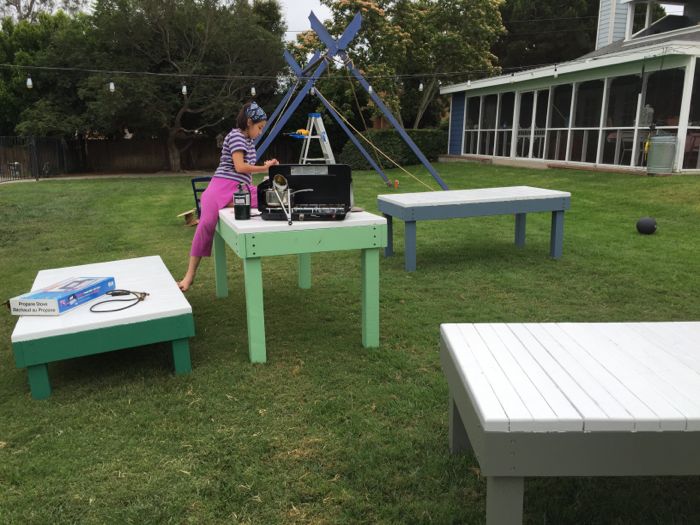
Together, Maria and I made seventy-six fire starters. And we still have wax, and definitely plenty of wood shavings for more! Alex put together some logs, and we tested one out. The wick
is handy for lighting the fire starter. With kindling around the fire starter, the slow burning wax and sawdust keep a consistent heat so the kindling can get the logs burning. It works like a charm!
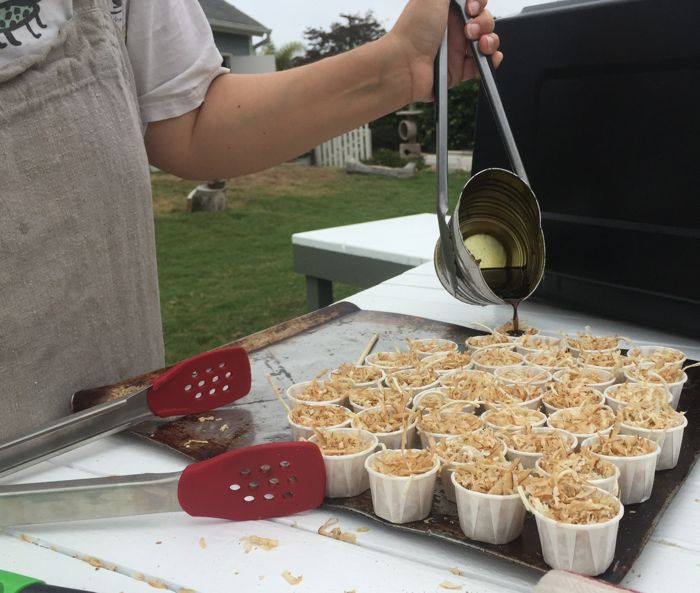
Double boiler? Yes, a coffee can, squeezed for convenient pouring, works nicely.
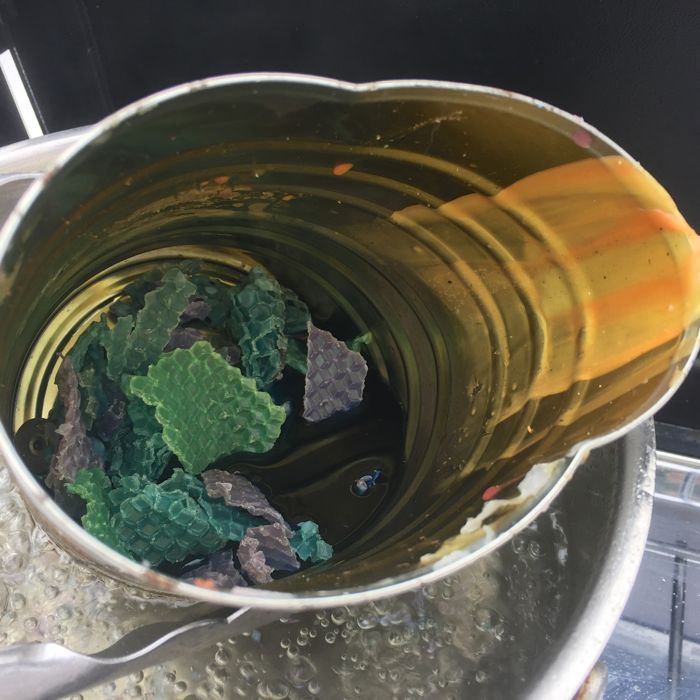
Check out our blues!
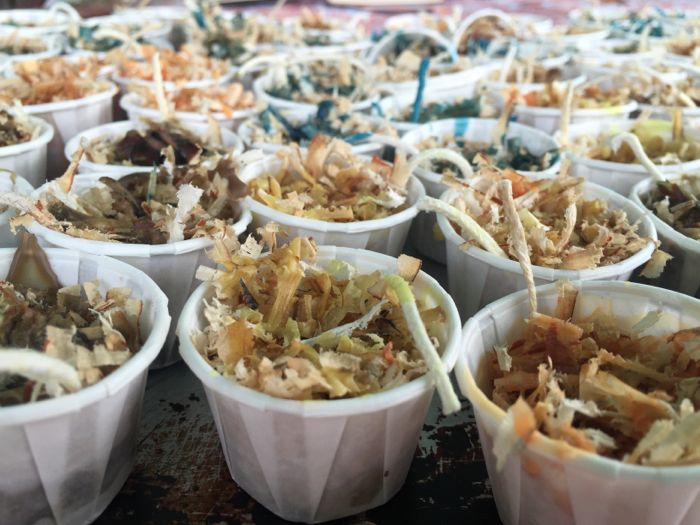
Seventy-six! They smell good, too, with the pine shavings, and honey.
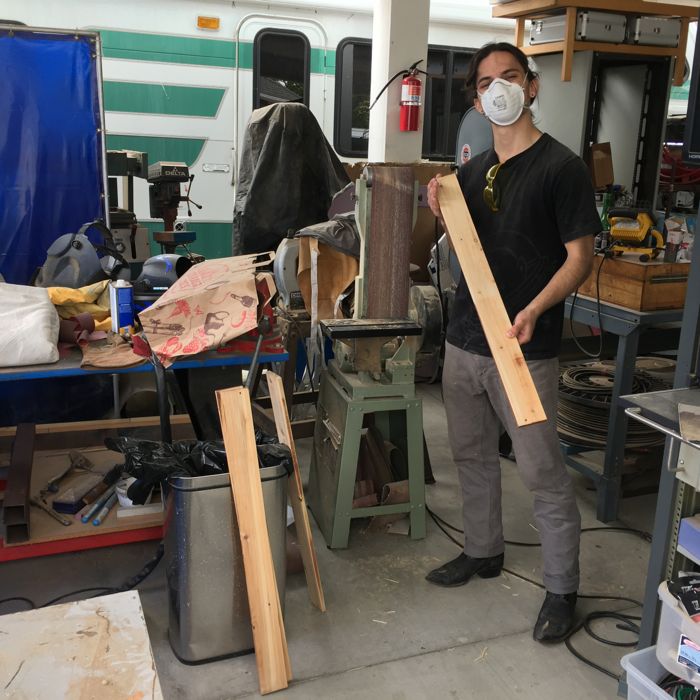
And while Maria and I were engrossed in our industry, James, Alex and William continued in theirs.
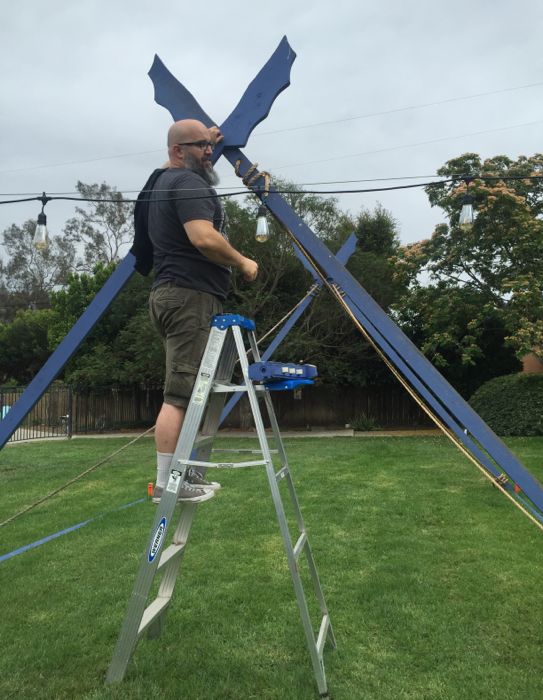
Geoff replaced ropes on the tent, and checked all the repairs and new dowels Alex used to repair the Viking tent (another victim of rough winter weather!) William and Alex painted details on
the dragon heads. They look fantastic. Paul and I returned from an administrative meeting for the
Maker Faire, pumped and inspired and so we got right back to work at actual Making.
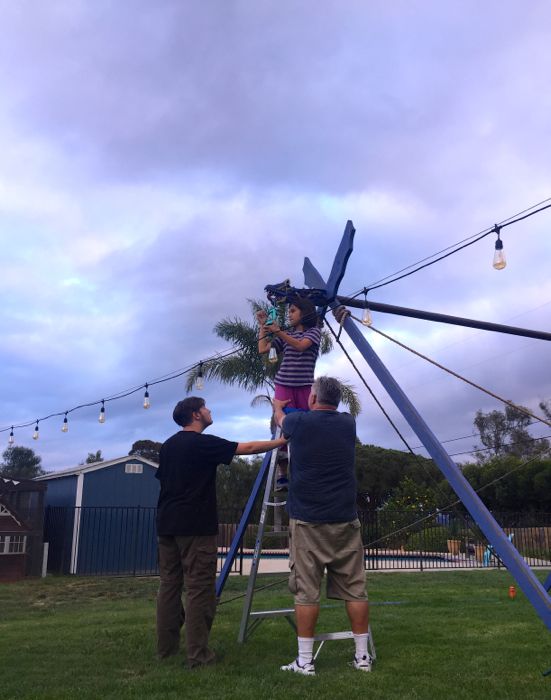
Making doesn't have to be complicated, or brought to a Faire. It doesn't have to be technical, or documented. What I love the most about what we do, is that it brings us together, sometimes just two of us, or only our immediate family, but often with friends, and we find a higher purpose, learn, teach, grow, and feel inspired to achieve meaningful, purposeful, good things. Light is good. Smiles are good. Laughter is good. Making is good.